CB-0034062-C GE
PCB-0034062-C represents the model or code of an electronic product, and parameter information may vary depending on the product. Generally speaking, the following are possible parameter information:
1. Size: includes information on the length, width, and height of the product.
2. Material: Describe the materials used in the product, such as metal, plastic, etc.
3. Weight: The weight of the product.
4. Power Requirements: Describe the power standards required for the product, such as voltage, frequency, etc.
5. Port/Interface: Describe the different interfaces or port types provided by the product, such as USB, HDMI, etc.
6. Processor: Describe the type, frequency, and other information of the processor installed on the product.
7. Storage capacity: Describe the storage capacity of the product, such as memory, disk, etc.
8. Operating System: Describe the operating system used by the product, such as Windows, iOS, etc.
9. Network Connection: Describe the types of network connections supported by the product, such as wireless network (Wi Fi), Bluetooth, etc.
10. Other features: such as the product’s sound input and output, graphics processing ability, camera, etc
INDRAMAT PROGRAMMIERMODUL DSM 2.1-S11-01.RS
INDRAMAT DDS03.2-W030-B DDS03.2W030-B DDS 03.2-W030-B
Indramat Profibus Interface CDB01.1C-PB-ENS-ENS-EN2-MEM
Indramat Power Supply TVM-1.2-050-W0-220V
INDRAMAT Servo Controller TDM-1.2-100-300-W1-S102
INDRAMAT AC-Servo Bleeder TBM TBM-1.2-040-W1
INDRAMAT Servo Controller TDM2.1-30-300-W0 NEUWERT
Indramat DLC 1.1 9BA6 DA01.1-01.8
The constant voltage frequency ratio control method for permanent magnet synchronous motors is similar to the constant voltage frequency ratio control method for AC induction motors.It controls the amplitude and frequency of the motor input voltage to change simultaneously,resulting in a constant magnetic flux of the motor.The constant voltage frequency ratio control method can adapt to the requirements of a wide range of speed control systems.
The biggest advantage of the constant voltage frequency ratio control method is that it can still achieve a certain control accuracy without feedback on physical signals such as current,voltage,or position.The constant voltage frequency ratio control method has a simple control algorithm and low hardware cost,and has been widely used in the field of general frequency converters.The disadvantages of the constant voltage frequency ratio control method are also obvious.Due to the lack of feedback on speed,position,or any other signals during the control process,it is almost impossible to obtain the operating status information of the motor,let alone accurately control the speed or electromagnetic torque.The system performance is average,and the dynamic response is poor,especially when the given target speed changes or load suddenly changes,it is easy to cause problems such as out of step and oscillation.Obviously,this control method cannot control torque and excitation current separately,and there may be large excitation current during the control process,which affects the efficiency of the motor.Therefore,this control method is commonly used in general frequency converters with lower performance requirements,such as air conditioning,conveyor belt drive control in assembly lines,energy-saving operation of water pumps and fans,etc.
Direct Torque Control Technology of Permanent Magnet Synchronous Motor
Direct Self Control(DSC)constructs flux and electromagnetic torque models on the stator stationary coordinate system,and controls the electromagnetic torque and stator flux by applying different voltage vectors.The direct torque control method has the advantages of simple algorithm and good torque response,therefore,it has been widely used in situations where high transient torque response is required.
Due to the inherent drawbacks of control,the direct torque control method has low control frequency and large torque ripple at low speeds.Therefore,reducing torque ripple at low speeds has become a research hotspot in direct torque control methods.Sun Xiaohui et al.optimized the voltage vector action time to reduce torque ripple at low speeds,achieving good results.D.Casadei et al.applied the direct torque control method to the control of AC induction motors based on discrete space vector modulation technology,reducing torque ripple.
Vector Control Technology of Permanent Magnet Synchronous Motor
Vector control technology was born in the early 1970s.The vector control system of permanent magnet synchronous motor refers to the control strategy of DC motor,and uses coordinate transformation to decompose the collected three-phase stator current,flux,and other vectors of the motor into two components according to the direction of the rotor flux,which is a rotating vector.One is along the direction of the rotor flux,called the direct axis excitation current;The other perpendicular to the direction of the rotor flux is called the quadrature axis torque current.Adjust the excitation current and torque current according to different control objectives,thereby achieving precise control of speed and torque,and achieving good steady-state and dynamic response characteristics of the control system.
According to different control objectives,vector control algorithms for permanent magnet synchronous motors can be divided into the following types:id=0 control,maximum torque/current control,weak field control,etc.These performance indicators are acceptable
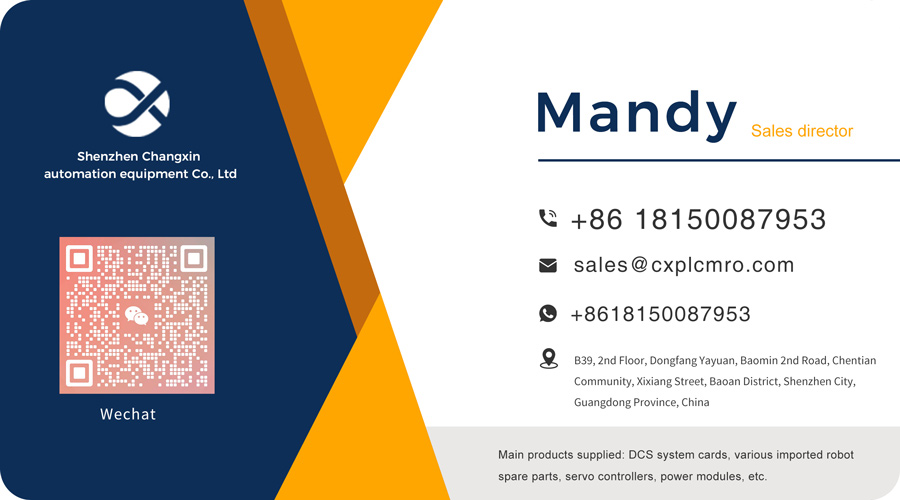
Reviews
There are no reviews yet.