NT23-050-S-RM060-6
The product parameters of the H2310240032X512 RELIANCE model are as follows:
-Model: NT23-050-S-RM060-6
-Input power supply: AC 100V-240V
-Output voltage: DC 5V
-Output current: maximum 0.5A
-Working temperature: 0 ℃ to 40 ℃
-Storage temperature: -20 ℃ to 85 ℃
-Shell material: plastic
-Size: 60mm x 25mm x 15mm
-Weight: approximately 20 grams
-Interface type: Micro USB
-Safety protection functions: overload protection, short circuit protection, overvoltage protection, overcurrent protection
-Scope of application: Can be used for charging and power supply of devices such as mobile phones, tablets, Bluetooth headphones, etc
ASEA BROWN BOVERI 57360001-KG/8 USPP 57360001KG8
ASEA BROWN BOVERI 57360001-A/5 USPP 57360001A5
ASEA BROWN BOVERI 57360001-A/6 USPP 57360001A6
ASEA BROWN BOVERI 52614759 NSFP 52614759
ASEA BROWN BOVERI ACS800-U1-0140-5-B056-L503-P901 USPP
ASEA BROWN BOVERI GNT2009459R0007 NSFP GNT2009459R0007
H2310240032X512 RELIANCE In order to improve the torque characteristics of the motor, many scholars and research institutions have made bold attempts and innovations in the structural design of permanent magnet synchronous motors, and have made many new progress. In order to solve the contradiction between slot width and tooth width, transverse flux machine technology has been developed. The armature coil and tooth slot structure are vertical in space, and the main magnetic flux flows along the axial direction of the motor, improving the power density of the motor; Adopting a double-layer permanent magnet arrangement increases the quadrature axis conductivity of the motor, thereby increasing the output torque and maximum power of the motor; Change the stator tooth shape and magnetic pole shape to reduce torque ripple of the motor, etc.
Weak magnetic expansion ability
After adopting weak magnetic control, the operating characteristics of permanent magnet synchronous motors are more suitable for the driving requirements of electric vehicles. Under the same power requirements, the inverter capacity is reduced and the efficiency of the drive system is improved. Therefore, permanent magnet synchronous motors for electric vehicle driving generally use weak magnetic field expansion. For this reason, domestic and foreign research institutions have proposed various solutions, such as adopting a double stator structure and using different windings at different speeds to maximize the utilization of the permanent magnet magnetic field; Adopting a composite rotor structure, the rotor adds a reluctance section to control the reactance parameters of the motor’s direct and quadrature axes, thereby increasing the motor’s speed expansion ability; The stator adopts deep grooves to increase the direct axis leakage reactance and expand the speed range of the motor.
Motor Control Theory
Due to the nonlinear and multivariable characteristics of permanent magnet synchronous motors, their control difficulty is high, and the control algorithm is complex. Traditional vector control methods often cannot meet the requirements. For this reason, some advanced control methods have been applied in permanent magnet synchronous motor speed control systems, including adaptive observers, model reference adaptation, high-frequency signal injection method, fuzzy control, genetic algorithm and other intelligent control methods. These control methods do not rely on the mathematical model of the control object, have good adaptability and robustness, and have unique advantages for nonlinear systems such as permanent magnet synchronous motors.
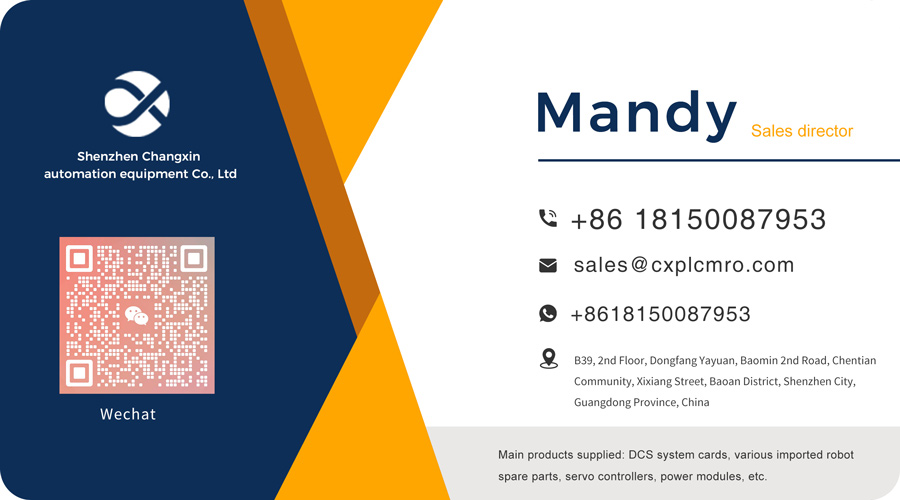
Reviews
There are no reviews yet.