ANR1250 PANASONIC
Product number ANR1250
Part number ANR1250
Measure center to center distance of 50 millimeters 1.969 inches
Measurement range plus or minus 10 millimeters plus or minus 0.394 inches
Light source laser diode (peak emission wavelength: 650 nm 0.026 mil)
Light source: pulse width/maximum output/laser level 15 micros (duty cycle 50%)/1.6 mW (peak)/2 levels (IEC 60825-1), (Level II is applicable for FDA compliant types)
Spot diameter (representative value of distance from measurement center) is approximately 0.6 x 1.1 millimeters 0.024 x 0.043 inches
Resolution (2 Sigma): 10Hz 1 micron 0.039 million
Resolution (2 Sigma): 100Hz 3.5 microns 0.138 million
Resolution (2 Sigma): 1kHz 10 microns 0.394 million
Within 0.2% of the linear error FS
(Note) White ceramics are the object of this value.
Protection (excluding connectors) IP67 (International Electrotechnical Commission)
Environmental illumination (incandescent lamp) 3000 liters × below
Net weight: Sensor head (including cable): approximately 240 g, middle cable: approximately 130 g
Insulation resistance (initial) between external DC input and sensor metal parts (excluding connector metal parts) 20 MOhm or higher (at 500 V DC megohmmeter)
Withstand voltage (initial) between external DC input and sensor metal parts (excluding connector metal parts) AC 500 V for 1 minute
Vibration resistance (screw installation) 10 to 55 Hz (1 cycle/minute) dual amplitude 1.5 mm 0.059 inches, two hours each in X, Y, and Z directions
Impact resistance (screw installation) above 20G, 3 times in X, Y, and Z directions
Environmental temperature 0 to+50 ° C+32 to+122 ° F
Storage environment temperature -20 to+70 degrees Fahrenheit -4 to+158 degrees Fahrenheit
Environmental humidity 35% to 85% RH (no condensation)
REXROTH INDRAMAT MAC112D-1-ED-2-C/130-A-0 Servomotor
REXROTH INDRAMAT MHD112C-024-NG0-AN Servomotor
Indramat Servo Motor MKD MKD090B-058-KP1-KN
Indramat Rexroth PPC-R02.2N-N-Q1-T2-NN-FW
Indramat 112D-0-FD-2-C/130-A-2/S013 Servomotor
Indramat bedieneinheit BTV20 BTV20.2CA-64B-10C-D-FW
INDRAMAT AC-SERVOANTRIEBSMODUL TDA 1.3-100-3-A00
Motors are devices that convert electrical energy into mechanical energy. They are made by utilizing the phenomenon of energized coils rotating under force in a magnetic field and are distributed among various users. Motors are divided into DC and AC motors according to the different power sources used. Most of the motors in the power system are AC motors, which can be synchronous or asynchronous (the stator magnetic field speed of the motor does not maintain synchronous speed with the rotor rotation speed). The electric motor mainly consists of a stator and a rotor. The direction of the force acting on an energized wire in a magnetic field is related to the direction of the current and the direction of the magnetic induction line (magnetic field direction). The working principle of an electric motor is the effect of a magnetic field on the force acting on the current, causing the motor to rotate.
It is a machine that converts electrical energy into mechanical energy. Usually, the working part of an electric motor rotates, and this type of motor is called a rotor motor; There are also linear motors that move in a straight line, called linear motors. Electric motors can provide a wide range of power, from milliwatts to tens of thousands of kilowatts. The use and control of electric motors are very convenient, with the ability to self start, accelerate, brake, reverse, and hold, meeting various operational requirements; The working efficiency of the electric motor is high, and there is no smoke or odor, which does not pollute the environment, and the noise is also low. Due to its series of advantages, it is widely used in various fields such as industrial and agricultural production, transportation, national defense, commercial and household appliances, medical electrical equipment, etc.
The most widely used among various electric motors is AC asynchronous motor (also known as induction motor). It is easy to use, reliable to operate, inexpensive, and structurally sturdy, but has a low power factor and difficult speed regulation. Large capacity and low speed power machines commonly use synchronous motors (see synchronous motors). Synchronous motors not only have a high power factor, but their speed is independent of the load size and only depends on the grid frequency. Work is relatively stable. DC motors are commonly used in situations where wide range speed regulation is required. But it has a commutator, which is complex in structure, expensive in price, difficult to maintain, and not suitable for harsh environments. After the 1970s, with the development of power electronics technology, the speed control technology of AC motors has gradually matured, and equipment prices have been decreasing, which has begun to be applied. The maximum output mechanical power that a motor can withstand under the specified operating system (continuous, short-term, intermittent cycle) without causing overheating of the motor is called its rated power. When using it, attention should be paid to the regulations on the nameplate. When the motor is running, attention should be paid to matching its load characteristics with the characteristics of the motor to avoid speeding or stalling. There are many speed control methods for electric motors, which can adapt to the requirements of different production machinery speed changes. The output power of a general electric motor varies with the speed during speed regulation. From the perspective of energy consumption, speed regulation can be roughly divided into two types: ① maintaining the input power unchanged. Adjust the output power to adjust the speed of the motor by changing the energy consumption of the speed control device Control the input power of the motor to adjust its speed.
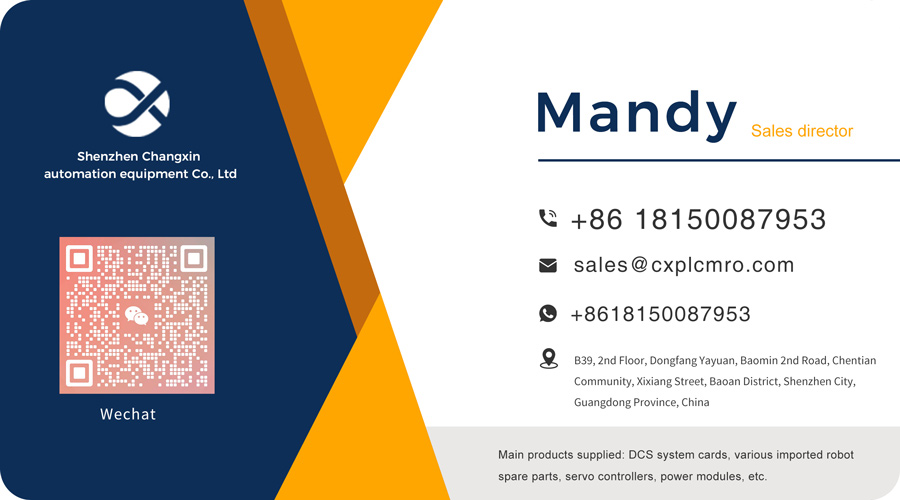
Reviews
There are no reviews yet.